Key Considerations in Refractories
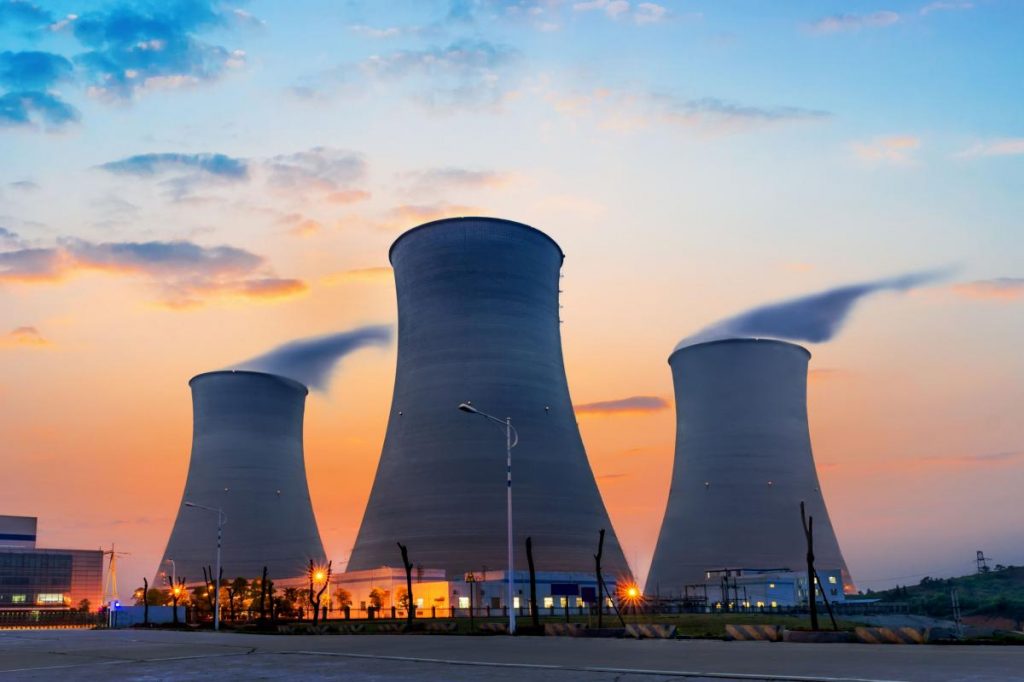
Refractories are a vital component of industrial manufacturing, and are used in every type of industrial process that utilises heat. They have been referred to as the ‘backbone of industry’, they are commonly used during the heat and chemical processing of all commodities such as cars, buildings, transportation infrastructure, etc.
Refractory refers to a variety of materials that are non-metallic and heat resistant
Refractories ought to withstand significant stress caused by heat and corrosion by chemical agents, and contain substances at high temperatures. Refractories is a substantial investment for many industrial facilities, and poor selection decision can be a liability to organisation.
Before product selections or installation decisions are made, there are a couple of things to take note: –
- Temperature of the manufacturing process
Refractories are used with heating applications that generate temperatures from 1000 Fahrenheit to 3000 Fahrenheit. There are three classifications of refractories based on temperature.
– Normal refractory (up to 1780 Fahrenheit) – typically fire clay that cover processes such as melting aluminum
– High refractory (1780 Fahrenheit – 2000 Fahrenheit) –cromite-based refractories that cover processes like melting copper
– Super sonic refractory (more than 2000 Fahrenheit) – zirconia-based refractories that cover processes like melting iron
- Chemical composition and resistance
There are different types of materials that be used and combined to create refractories that can withstand the different chemical processes. Refractories are nonmetallic in order to withstand the high temperatures.
– Acidic refractory – They are not affected by acids and include substances such as silica, alumina and fire clay brick refractories.
– Neutral refractory – used when the slags and atmosphere are either acidic or basic and chemically stable to both acids and bases
– Basic refractory – used on areas where slags and atmosphere are basic. They are stable to alkaline materials but are reactive to acids
- Size and shape
The size and shape of a refractory is dependent on how they are going to be used. There are three different types of refractory materials: –
– Bricks – used in most furnaces
– Fiber blanks – used for linings
– Monolithic refractories – shaped depending on how it is going to be used
API 936 Refractory Inspection is a 3-day certification course that provides an intensive overview of refractory materials used in refineries, power generation and petrochemical facilities consistent with API 936 body of knowledge. The course will cover the material, equipment and personnel qualification requirements along with procedures and responsibilities for quality control inspection personnel, and many more. For more information, please visit us at http://www.opuskinetic.com/training or contact us at info@opuskinetic.com
Opus Kinetic believes that people are why organisations are successful, and giving people the knowledge to perform well at their job is integral for success. We pride ourselves as the premier provider of knowledge, offering acclaimed in-house training, leadership training courses, oil and gas training courses, courses that target health safety and environment, etc. Our training courses are well researched and updated with the latest industry trends. For more information on our professional training programs, you can visit us at http://www.opuskinetic.com/training.