Shutdown & Turnaround of Refineries
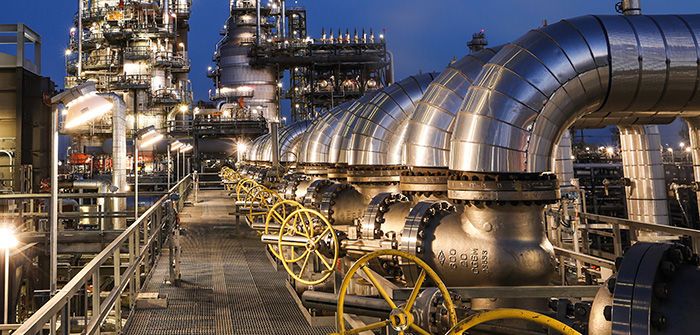
Oil and gas accounted for bulk of energy consumption all over the world and are mainly used for transportation and electricity generation. Although there is a transition from fossil fuels usage to alternative energy, new infrastructure are still unable to process supply that can meet the existing demand, hence there is still a high reliance on oil and gas. Shutdowns and turnarounds are sizable projects that have to be executed under strict time constraints with severe financial impacts when face with project delays.
Shutdown
Refineries take crude oil and refine it into gasoline, diesel and other petroleum products. Like all machineries, they call for maintenance, and in this context, a shutdown will occur. Several conditions can lead to a refinery shutdown, planned or unplanned. According to the US Department of Energy’s Energy Assurance Daily, there were over 1700 refinery shutdowns from 2009 to 2012 with 46% of them were caused by mechanical breakdowns, 23% by maintenance, 19% by electrical disruptions and power failures, and 12% by other causes such as fire accidents. The duration of a shutdown can range from a couple of hours to weeks, with 92% of them being unplanned.
A shutdown is a disruption in the refining process. An unplanned shutdown can cost companies millions due to production lost. On top of that, if the shutdown is caused by accidents, it may result in injuries or even fatalities in more severe cases. A shutdown can also increase the chance of fugitive emissions and pollution.
Turnaround
Refineries go through a turnaround every three to five years, and the typical period of advance planning for a turnaround is one or two years or more, depending on whether major processing or equipment changes are needed. Similarly, completion time for turnarounds vary from a few weeks to a few months or more, depending on the extent of the project or the problems that occur during the turnaround period.
Activities during a planned turnaround might include[1]:
- Routine inspections for corrosion, equipment integrity or wear, deposit formation, integrity of electrical and piping systems
- Special inspections (often arising from anomalies in the prior operating period) of major vessels or rotating equipment or pumps to investigate for abnormal situations
- Installation of replacement equipment for parts or entire pumps or instruments that wear out
- Replacement of catalysts or process materials that have been depleted during operations.
Improvement activities could include:
- Installation of new, upgraded equipment or technology to improve the refinery processing
- Installation of new, major capital equipment or systems that may significantly alter the refinery process and product output
Turnarounds are in place to solve maintenance issues that cannot be addressed when the plant is in operation, it is also a good opportunity for internal inspection of equipment. However, turnarounds are large scale and expensive. For instance, a 29-day turnaround at Valero’s St. Charles refinery cost $39 million and used about 1800 outside contractors. It was also estimated that Valero lost between $1.2 million and $3 million each day if the turnaround went beyond its projected time. Henceforth, good planning and efficient allocation of resources are heavily emphasised upon during the planning stage of a turnaround.
Advanced Shutdown Turnaround and Start-Up is a 3-day course designed to allow participants the different stages of Shutdown, Turnaround and Start-up. The planning, preparation and execution of a turnaround is a complex process and demands a highly effective strategy, control and high details. The course undertakes an interactive approach with exercises and case studies. For more information, please visit us at http://www.opuskinetic.com/training or contact us at info@opuskinetic.com
Opus Kinetic believes that people are why organisations are successful, and giving people the knowledge to perform well at their job is integral for success. We pride ourselves as the premier provider of knowledge, offering acclaimed in-house training, leadership training courses, oil and gas training courses, courses that target health safety and environment, etc. Our training courses are well researched and updated with the latest industry trends. For more information on our professional training programs, you can visit us at http://www.opuskinetic.com/training.
[1] Taken from Refinery Outages: Description and Potential Impact on Petroleum Product Prices by Energy Information Adminstration, US Department of Energy, March 2007