How Leadership In Process Safety Is The Key to Successful PSM Implementation
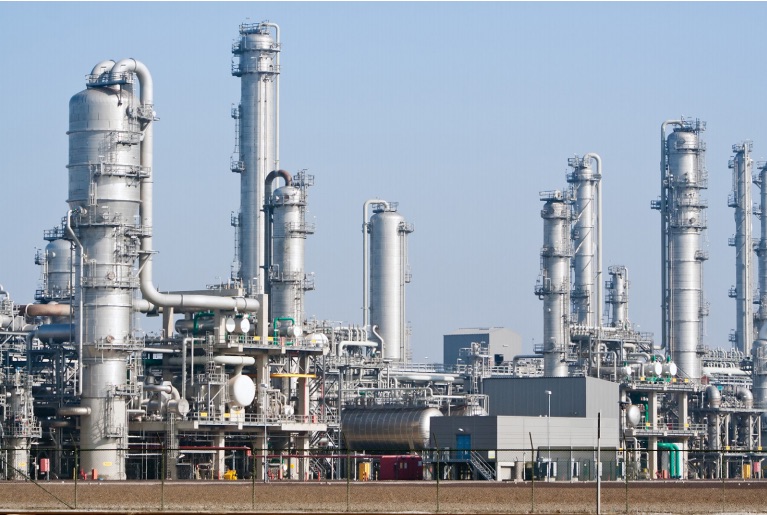
Process safety incidents can induce an enormous loss of capital and business continuity, while negatively affecting the company’s reputation. As companies are responsible for all onsite workers, companies will need to know how to guarantee their safety while ensuring the facility is always operating at maximum safety. In addition, companies will need to know how to ensure acceptable risk level through a comprehensive management system and to ensure that it is fit for purpose and suits the Process Safety Management (PSM) system.
If an organisation’s PSM system is to be successful and sustainable, it requires the commitment of the entire workforce, starting at the top. Process safety leadership is the key to successful PSM implementation on a global scale. Without detailed policies and effective monitoring and management systems, the risk of a major accident and its consequences increases sharply. Whilst it is essential that competent personnel are charged with managing process safety, experience has shown that if not properly directed, this often leads to reactive compliance.
The findings of the study conducted by The US Center for Chemical Process Safety (CCPS) (2007) revealed while there are different global regulatory requirements, the same safety issues were raised. The 4 common issues were:
- Commitment to Process Safety
- Understanding Hazards and Risks
- Managing Risks
- Learning From Experience
The most concerning issue lies with the company’s commitment to process safety. It provides the foundation for the PSM system and needs to be considered in process safety culture, compliance with standards, competency, workforce involvement and stakeholder outreach, Center for Chemical Process Safety (CCPS) (2007).
Key findings covered:
Recognition that organisations need to ensure a policy is in place, which fits with existing policies, and promotes:
- Recognition that policies and procedures are necessary
- Common objectives and targets
- A shared sense of vulnerability
- Prioritisation of process safety over production
- Appropriate and proportionate use of risk assessment
- Open communications
- Continuous improvement in process safety
Key to effective PSM culture is leadership from the top, ensuring:
- A sponsor is determined at board / senior level and this is communicated throughout the workforce
- Visibility of the senior management team focussing on process safety
- Process safety is given at least equal importance of other business areas such as financial control and productivity. Engagement of the hearts and minds of an organisation are key to sustaining a positive process safety culture throughout the entire workforce.
This can be achieved through:
- Setting of standards, objectives and targets
- Structured training
- Follow-up through appraisal process
- Visual management of process safety
- Management, operations and engineering
- Programme monitoring, audit and review
To read more about the remaining factors and the full article: PROCESS SAFETY LEADERSHIP IS THE KEY TO SUCCESSFUL PSM IMPLEMENTATION BOTH IN THE UK AND ON A GLOBAL SCALE
Excellence in Plants Process Safety & Risk Management is a 3-day training course held from 26 – 28 November 2018 (Kuala Lumpur) designed to provide an insight into the major drivers into fire and explosion hazard risk, and the various methods of preventing and mitigating such risk. The course will discuss quantitative consequence analysis, such as vapor dispersion modeling, vapor cloud explosion modeling, fire modeling, and presents the details necessary to perform such analyses. In addition, it will focus on the fire and gas detection systems for offshore and onshore process areas, and how such systems can be used to lower the overall explosion risk to facilities.
Human Factors Engineering for Oil & Gas is a 3-day training course held from 22 – 24 October 2018 (Singapore), where delegates will be introduced to contemporary thinking related to Applied Human Factors and Safety in Design and illustrate, through numerous examples, why it’s critical to incorporate HFE into your own projects. The ideas you develop in this course will help you understand how design decisions affect human performance and ultimately operational performance. Case studies will be used with a detailed first-hand experience of how HFE was applied within real projects, to demonstrate the flexibility of the HFE processes to fit them to real work.
ALARP Principles & Guidelines is a 2-day training course held from 29 – 30 November 2018 (Kuala Lumpur) designed for delegates to gain the key concepts of ALARP principles and the fundamental approaches for its applications. The course will cover the HSE principles for Cost Benefit Analyses (CBA) in support of ALARP decisions and understand the approaches to good practice and to demonstrate ALARP using different decision making criteria.
For more information, please contact us at info@opuskinetic.com.
Interested to read other related articles? Check out: 3 Major Process Safety Incidents since 2010
Opus Kinetic believes that people are why organisations are successful, and giving people the knowledge to perform well at their job is integral for success. We pride ourselves as the premier provider of knowledge, offering acclaimed in-house trainings, and many others professional training courses spanning from various industries. Our training courses are well researched and updated with the latest industry trends. For more information on our professional training programs, visit us at http://www.opuskinetic.com/training.