Managing Human Failures for Human Factors Engineering
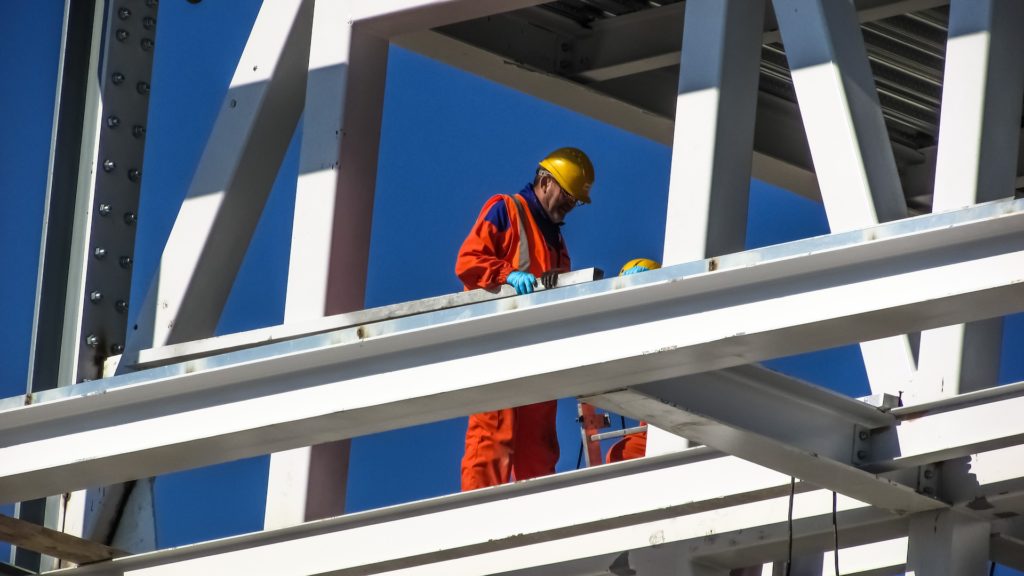
Estimated reading time: 5 minutes
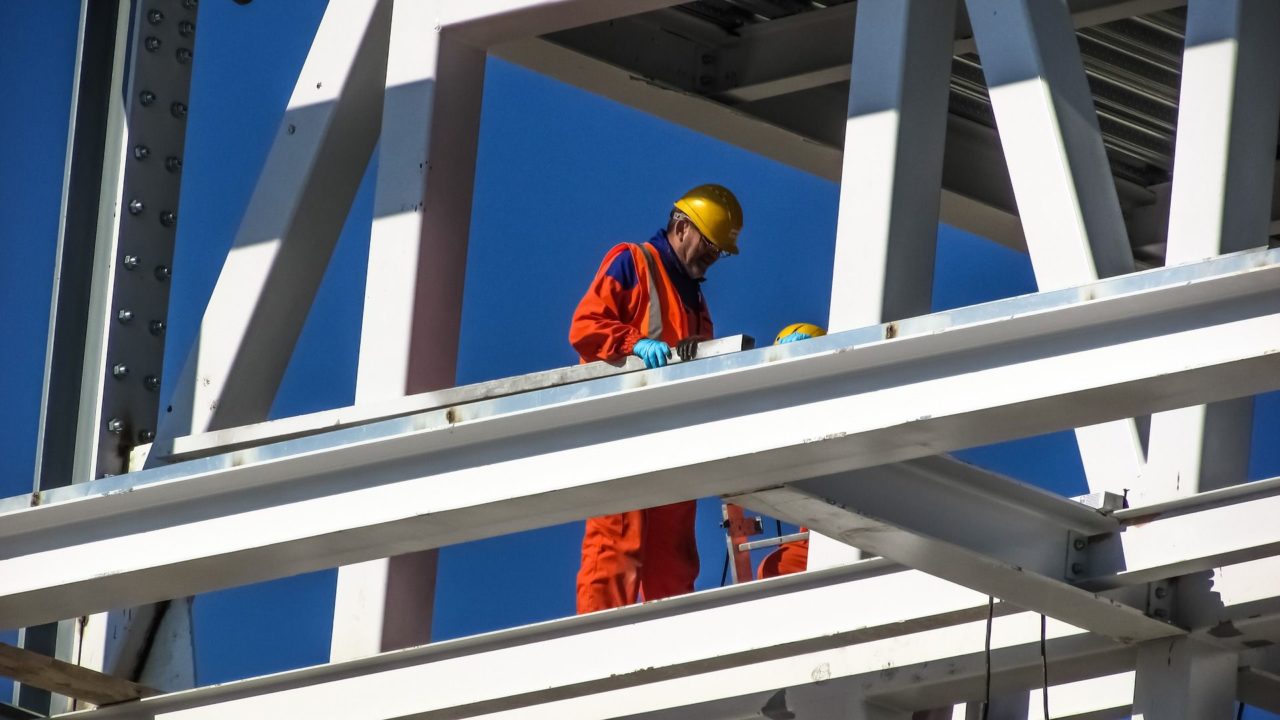
Human Factors Engineering for Oil & Gas
Everyone can make errors no matter how well trained and motivated they are. However, in the workplace, the consequences of such human failure can be severe. Analysis of accidents and incidents shows that human failure contributes to almost all accidents and exposures to substances hazardous to health. Many major accidents were initiated by human failure. In order to avoid accidents and ill-health, companies need to manage human failure by properly integrating human factors in preparation for safety case.
When preparing for safety case assessment, there is a human factors aspect to show that measures have been taken to prevent foreseeable human failures that could lead to major accidents. As safety measures improve, there is a significance increase in the role human factors play in producing these reports.
Furthermore, according to HSE, there are several key principles in managing human failure. These principles include:
- Human failure is normal and predictable. It can be identified and managed.
- Industry should tackle error reduction in a structured and proactive way, with as much rigour as the technical aspects of safety. Managing human failure should be integral to the safety management system.
- A poorly designed activity might be prone to a combination of errors and more than one solution may be necessary.
- Involve workers in design of tasks and procedures.
- Risk assessment should identify where human failure can occur in safety critical tasks, the performance influencing factors which might make it more likely, and the control measures necessary to prevent it.
- Incident Investigations should seek to identify why individuals have failed rather than stopping at ‘operator error’.
Bearing in mind these key principles, there are several points to take note of when managing human failure. Although sufficient training have been provided, staff are still prone to mistakes and may inappropriately apply techniques, not follow procedures or fail to detect problems. Hence, it is important to factor for the human performance at all risk assessments.
Useful links: Safety Case Regime for MHIs
Human Factors Engineering for Oil & Gas is a 3-day training course held from 27- 29 March 2019 (Kuala Lumpur) and 1-3 April 2019 (Singapore) based on the well-established discipline of Human Factors Engineering (HFE). The course will introduce delegates to contemporary thinking related to Applied Human Factors and Safety in Design and illustrate, through numerous examples, why it’s critical to incorporate HFE into your own projects. Case studies will be used to provide delegates with a clear understanding of what can go wrong without HFE and that its inclusion leads to improved operational performance for the plants you’re using and designing.
27 – 29 March 2019 (Kuala Lumpur):
Interested to read other articles? Check out: Increasing Role of Human Factors in Safety Management
Opus Kinetic believes that people are why organisations are successful, and giving people the knowledge to perform well at their job is integral for success. We pride ourselves as the premier provider of knowledge, offering acclaimed in-house trainings, and many others professional training courses spanning from various industries. Our training courses are well researched and updated with the latest industry trends. For more information on our professional training programs, visit us at http://www.opuskinetic.com/training.