HAZOP Studies: Advantages and Disadvantages of its Use
Average Reading time 7 minutes
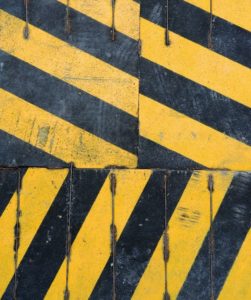
<HAZOP Studies: Advantages and Disadvantages of its Use>
HAZOP, which stands for a Hazard and Operability Study, is a systematic way to identify possible hazards in a work process. With the use of this study, processes are broken down into steps, and variations in work parameters is scrutinised closely to see what could go wrong at each step of the process. It is important for process engineers to understand when HAZOP studies should be used hence we will look at advantages and disadvantages of the use of HAZOP studies.
The HAZOP approach is commonly used with chemical production and piping systems, where miles of pipes and numerous containers can result in logistical headaches. It is best suited for assessing hazards in facilities, equipment, and processes and can assess systems from multiple perspectives.
HAZOPs are not the best approach for every circumstance, and it is important to understand the benefits as well as the costs and limitations of the method before making the decision to use it in a circumstance. Unlike its other Process Hazard Analysis (PHA) method counterparts like Checklists and What-ifs methods, HAZOP studies are used mainly in complex situations where the other PHA methods. Now let us dive deeper into the analysis of the HAOP methodology, and what it’s pros and cons are.
Advantages
Through careful scrutiny and consultation of sources like the Health and Safety Executive (HSE) , the following information lists the advantages that come from the use and implementation of a HAZOP study.
- Resultant analysis will be very highly structured, comprehensive and detailed. Since HAZOP studies usually have a systematic & comprehensive methodology, with a detailed plan for performing the technique available which systematically applies guide words and parameters to all the pipes and vessels in the process. This would explicitly identify the hazards, the potential failures, the potential causes of failure and the recommended actions to address. Making it clear for the readers to understand, since the analysis would be clearly documented.
- Since the HAZOP methodology does not require engineers to explicitly rate or measure the deviation probability of hazard occurrence, severity of impact, or the ability to detect, the HAZOP method is extremely useful when confronting hazards that are difficult to quantify. These hazards include,
- Hazards rooted in human performance and behaviours,
- Hazards that are difficult to detect, analyse, isolate, count, predict, etc
- HAZOP analysis requires input from a range of disciplines resulting in a more balanced analysis.
- This multidisciplinary team approach required from HAZOP encourages multiple viewpoints and ensures a broad range of potential concerns can input into the analysis.
- More simple and intuitive than other commonly used risk management tools
- HAZOP does not require considerable technical expertise for technique formulation.
- The process itself is relatively easy to understand and is not highly technical, therefore does not require extensive training for team members inputting into the analysis
- The HAZOP method has a built-in brainstorming methodology, which can help to detect problems early. Using the HAZOP method, emergency response processes are split into 5 main stages which help frame the thinking process. These 5 stages are
- Setting up emergency command posts
- Restricting access within, to and from the facility
- Muster and roll call
- Dealing with the incident
- Resumption of normal operations
Disadvantages
Since HAZOPs are not applicable for all situations, the following information lists the disadvantages that come from the use and implementation of a HAZOP study.
- The HAZOP analysis focuses on single failure conditions rather than on combinations of possible events leading to a resultant failure This would mean that the HAZOP analysis has no means to assess hazards involving interactions between different parts of a system or process. Additionally, since process failure often result from multiple failed inputs, HAZOP processes do not capture and analyse these scenarios.
- Most HAZOP analysis have no means to assess effectiveness of existing or proposed controls, based on its design. As such, process engineers will need to interface their HAZOP analysis procedures with other risk management tools like HACCP, to be able to carry out such functions.
- HAZOP process can be time consuming, can become overly detailed and complex and often requires some form of expert facilitation. Since the HAZOP reports are usually very detailed and complex, someone who does not have any background in process engineering will not be able to understand the jargon and information covered in the report without the aid of an expert. Additionally, most plants contain a large number of pipes and vessels each of which need to be examined by the application of the various guidewords and parameters, which makes it a very time consuming process.
- HAZOP relies heavily on “guide words” to progress the analysis. Since HAZOP reports identify deviations in processes using sets of “guide words” as a systematic list of deviation perspectives, it runs the risk of being missed by the HAZOP analysis. This is because, potential failures cannot always be linked to “guide words”.
- The HAZOP analysis requires more resources compared to the Checklist and What-if methods which are other PHA methods. This is because the HAZOP method, requires up-to-date process safety information and a multidisciplinary team who understands the processes well
Through this discussion of the advantages and disadvantages of the HAZOP study, it is important to note that while a HAZOP is not appropriate in all circumstances it is also one of the major benefits that can be used to help justify the cost and time investment. It also helps to avoid operating problems and can thus provide a clear return on the investment beyond the reduction in hazards.
To find out more about the various PHRA methods and learn more about process hazards and the various risk analysis that process engineers can adopt to attend courses such as TUV Rheinland Functional Safety, Process Hazard & Risk Analysis (PH & RA) Training, to understand and master process hazard analysis. To find out how you can conduct a successful HAZOP study do check out our other blog below too!