The 6 Main classifications of inventory
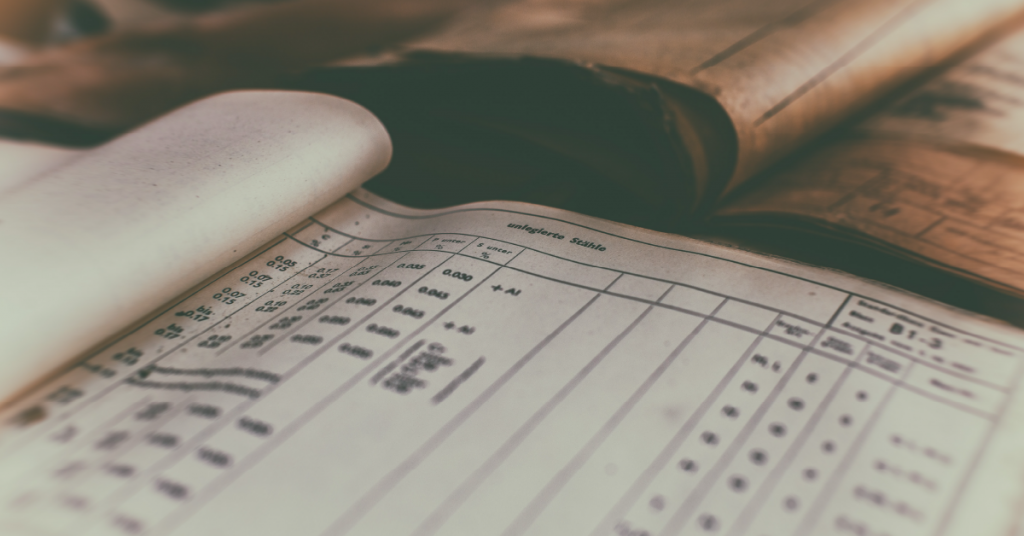
Average reading time 12 minutes
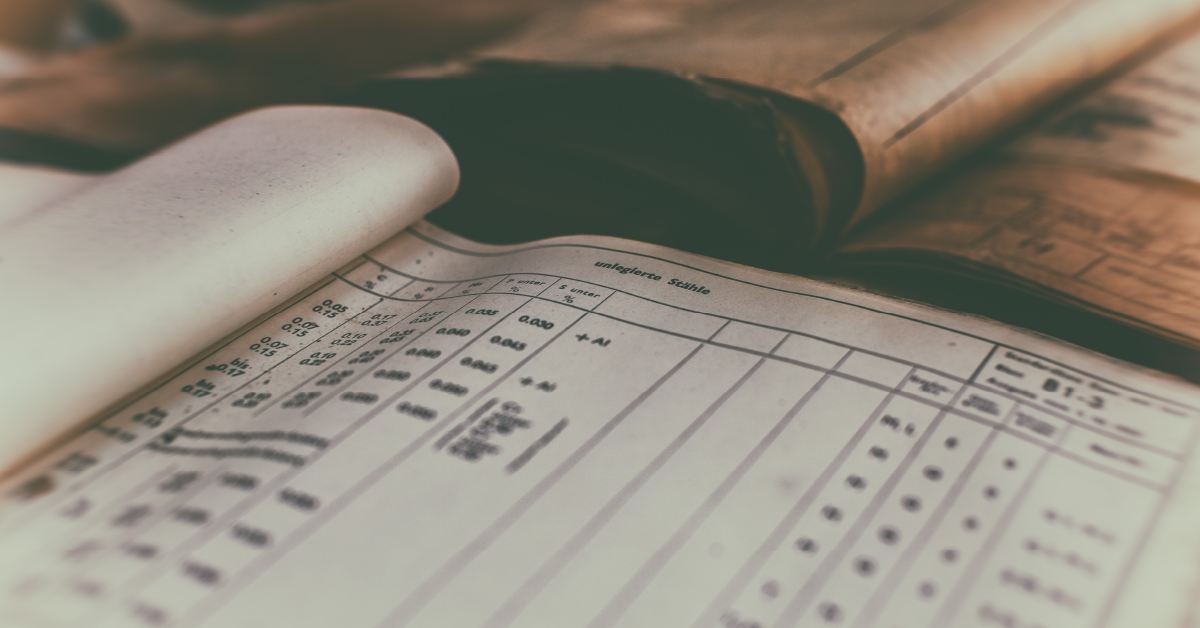
<The 6 Main classifications of inventory>
Inventory is a necessary evil in any organization engaged in production, sale or trading of products. In business, inventory may be defined as the goods held for sale in the ordinary course of business or the goods that are used to manufacture goods to be sold. Inventories usually make up a large part of the total current assets of a company. As such, it is usually important that directors and senior management understand the inner workings of the supply chain to improve their inventory management skills. We’ll cover the 6 main classification of inventory to help managers get a better understanding of inventory management.
Inventory in any organization can run in thousands of part numbers or classifications and millions of part numbers in quantity. Therefore, inventory is required to be classified with some logic to be able to manage the same. Inventories can be further classified according to the purpose they serve. Hence, the following lists the 6 main inventory classification that can aid in inventory management.
- transit inventory
- buffer inventory
- anticipation inventory
- decoupling inventory
- cycle inventory
- MRO goods inventory
Some of these are also known by other names, such as speculative inventory, safety inventory, and seasonal inventory.
TRANSIT INVENTORY
Transit inventories result from the need to transport items or material from one location to another, and from the fact that there is some transportation time involved in getting from one location to another. Since the inventory is still in-transit it is also called pipeline inventory and it is a crucial part of inventory management.
Merchandise shipped by truck or rail can sometimes take days or even weeks to go from a regional warehouse to a retail facility. Some large firms, such as automobile manufacturers, employ freight consolidators to pool their transit inventories coming from various locations into one shipping source. This is in order to take advantage of economies of scale. Of course, this can greatly increase the transit time for these inventories, hence an increase in the size of the inventory in transit.
BUFFER INVENTORY
Buffer inventory, also called buffer stock or safety stock, is a cushion of supply in excess of forecast demand. Inventory is sometimes used to protect against the uncertainties of supply and demand, as well as unpredictable events such as poor delivery reliability or poor quality of a supplier's products. These inventory cushions are often referred to as buffer inventory. Buffer inventory is any amount held on hand that is over and above that currently needed to meet demand.
Generally, the higher the level of buffer inventory, the better the firm's customer service. This is because maintaining a buffer inventory allows companies to reduce the probability that it will experience outages of desired goods. Thus, customers do not have to wait until the next order cycle, or even worse, leave empty-handed to find another supplier. Obviously, the better the customer service the greater the likelihood of customer satisfaction.
ANTICIPATION INVENTORY
Anticipation inventory is the stock of components, material, or goods kept at hand by a company or business to meet demand or to meet the shortfall caused by erratic production. Often, firms will purchase and hold inventory that is in excess of their current need in anticipation of a possible future event. Such events may include a price increase, a seasonal increase in demand, or even an impending labour strike. This tactic is commonly used by retailers, who routinely build up inventory months. Example will be before the demand for their products will be unusually high (i.e., at Halloween, Christmas, or the back-to-school season).
For manufacturers, anticipation inventory allows them to build up inventory when demand is low (also keeping workers busy during slack times) so that when demand picks up the increased inventory will be slowly depleted. In this case, the firm does not have to react by increasing production time (along with the subsequent increase in hiring, training, and other associated labour costs).
Therefore, the firm has avoided both excessive overtime due to increased demand and hiring cost. It also has avoided layoff costs associated with production cutbacks, or worse, the idling or shutting down of facilities. This process is sometimes called "smoothing" because it smoothens the peaks and valleys in demand, allowing the firm to maintain a constant level of output and a stable workforce.
DECOUPLING INVENTORY
Decoupling inventory involves separating inventory within a manufacturing process so that the inventory associated with one stage of a manufacturing process does not slow down other parts of the process. Production facilities rarely have machines in every process which produces at the same rate. In fact, one machine may process parts several times faster than the machines in front of or behind it. It also could be possible that through the plant, several machines are under repair or are undergoing some form of preventive maintenance.
Even so, this does not seem to interrupt the flow of work-in-process through the system. The reason for this is the existence of an inventory of parts between machines, a decoupling inventory that serves as a shock absorber, cushioning the system against production irregularities. As such it "decouples" or disengages the plant's dependence upon the sequential requirements of the system.
The more inventory a firm carries as a decoupling inventory between the various stages in its manufacturing system, the less coordination is needed to keep the system running smoothly. Naturally, an infinite amount of decoupling inventory would not keep the system running in peak form. A balance needs to be reached that will allow the plant to run relatively smoothly without maintaining an absurd level of inventory. The cost of efficiency must be weighed against the cost of carrying excess inventory so that there is an optimum balance between inventory level and coordination within the system.
CYCLE INVENTORY
Cycle stock inventory, also referred to as working stock, is the portion of inventory available to meet normal demand during a given period. Those who are familiar with the concept of economic order quantity (EOQ) know that the EOQ is an attempt to balance inventory holding or carrying costs with the costs incurred from ordering or setting up machinery. When large quantities are ordered or produced, inventory holding costs are increased, but ordering/setup costs decrease.
Conversely, when lot sizes decrease, inventory holding/carrying costs decrease, but the cost of ordering/setup increases since more orders/setups are required to meet demand. When the two costs are equal, the total cost is minimized. Cycle inventories result from this process. Usually, excess material is ordered and, consequently, held in inventory to reach this minimization point. Hence, cycle inventory results from ordering in batches or lot sizes rather than ordering material strictly as needed.
MRO GOODS INVENTORY
Maintenance, repair, and operating supplies, or MRO goods, are items that are used to support and maintain the production process and its infrastructure. Hence, MRO inventory keeps track of these operational items. These goods are usually consumed as a result of the production process but are not directly a part of the finished product. Examples of MRO goods include oils, lubricants, coolants, janitorial supplies, uniforms, gloves, packing material, tools, nuts, bolts, screws, shim stock, and key stock. Even office supplies such as staples, pens and pencils, copier paper, and toner are considered part of MRO goods inventory.
Inventory exists in various categories as a result of its position in the production process (raw material, work-in-process, and finished goods) and according to the function it serves within the system (transit inventory, buffer inventory, anticipation inventory, decoupling inventory, cycle inventory, and MRO goods inventory).
As such, the purpose of each seems to be that of maintaining a high level of customer service or part of an attempt to minimize overall costs.
To understand more about supply chain management, do read our other blogs below or visit some of our courses.
Interested to find out more?