How to Develop an Effective Maintenance and Reliability Program
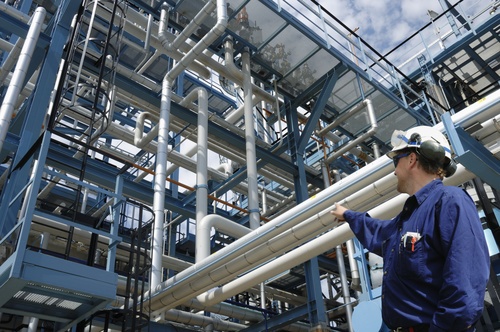
Estimated reading time: 6 minutes
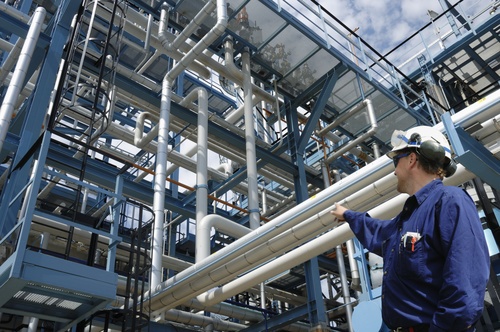
Advanced Reliability and Maintenance Programs
The effective maintenance management is a critical feature of plant operations, both in establishing the conditions for safe ongoing operation of the plant after commissioning, and in supporting the commercial success of the business. Ultimately, the contribution of a maintenance organisation can most effectively be measured in terms of its ability to generate sustained improvements with time in the total (fixed and variable) cost per unit volume of production.
An effective reliability program provides the appropriate maintenance on the right assets at the right time. Rather than performing a critical evaluation of their maintenance plans, many companies replace malfunctioning or out-of-date equipment with the latest technology. However, this is counterproductive as without an efficient maintenance program, the latest technology is not beneficial.
The goal of a maintenance and reliability program is to deliver a proper balance of maintenance activities – primarily those aimed at identifying impending failures – to allow for timely corrective actions. The optimal maintenance and reliability program for a plant provides the timely maintenance on the key assets. By identifying the right assets that are most important to the business, what should be done to restore or maintain reliability of those assets and at what frequency those actions should be taken, a maintenance organisation can become more effective and more efficient while reducing costs significantly.
The 6 key steps to establishing an effective maintenance and reliability program are:
- Create an outline of the organisation
- Develop a plan for improvement
- Prioritise plant assets
- Define maintenance requirements
- Allocate personnel resources and deploy tools
- Measure success and continuously improve
These steps act as the foundation to redefine the plant’s maintenance program and build an efficient program that improves reliability and availability of plant assets, at minimal costs.
- Create an outline of the organisation
A plant can get an understanding of the current status of its maintenance program in many ways, such as industry benchmarking, through surveys, or using a trial-and-error approach. One way is to measure performance against a set of best practices. This is also a way for management to get feedback on the issue affecting the organisation’s maintenance program.
Some examples of the key metrics that the assessment examines are:
- Work Processes (spare parts, work scheduling, work execution, work order close-out)
- Technology (work management systems, maintenance and diagnostics technologies, information integration systems)
- Management and Work Culture (benchmarking, goal setting)
- Expertise (work identification, training)
- Develop a plan for improvement
After assessment, the metrics that received the lower ratings present room for opportunities. An organisation can develop a plan to close the gaps and raise its performance on key metrics, thereby improving its overall performance. This step may include planning for training, developing and optimizing procedures, improving communications or integrating software systems. The plan should rank the plant’s assets based on how critical they are to the business, and then optimise the associated maintenance tasks based on those rankings.
- Prioritise plant assets
The next step is to carry out the plan, which starts with taking an unbiased look at the relative criticality of assets in an area or system. Operations and maintenance personnel should collaborate to define the basic functional systems and the associated assets that work together to achieve a specific function. There are various ranking systems to be applied for each asset, such as the Subsystem System-Criticality Ranking and the Asset Production-Criticality Ranking.
- Define maintenance requirements
A 2017 maintenance study found that 78% of facilities follow a preventative maintenance strategy, while 59% use a computerised maintenance management system. Either way, to ensure a viable maintenance strategy is in place, first examine the scheduled maintenance activities that are being performed. Make sure there is an appropriate balance of conditional inspections, pre-emptive replacements, monitoring technology applications and more. An example of an industry recognised maintenance strategy is reliability-centered maintenance (RCM).
- Allocate personnel resources and deploy tools
Next, determine the annual workload required to carry out the maintenance plan. The frequency and complexity of each task will determine how many man-hours are required for maintenance each month. If technology was implemented to optimise an existing strategy, the total workload might be reduced. In some cases, the technology may need to be re-allocated from low-criticality to assets to higher-criticality assets.
- Measure success and continuously improve
After evaluating and redefining the maintenance plan, a plant determines that it is operating at an average level. While the plant has achieved its goal of performing the right maintenance on the right assets, it is likely that the maintenance actions are performed too often. More can be done to increase the potential savings in performing maintenance eat longer or optimal intervals. Testing out the right intervals for maintenance is the easiest way to incur cost savings and improve productivity levels.
Without a plan or process to manage reliability and maintenance programs, work processes may never be improved. Having an established and efficient reliability program can bring about as much as a 7:1 return in the first year alone. These savings are typically comprised of reductions in overtime, reductions in equipment expenditures and more important, a decrease in unscheduled or unplanned downtime. When it comes to plant and process equipment, improving reliability is the key to ensuring uninterrupted production and lowering the total cost of ownership. It also helps meet health and safety standards and reduces environmental impact by limiting the risk of accidents.
![]() |
![]() |