Why is Maintenance and Reliability Management Important?
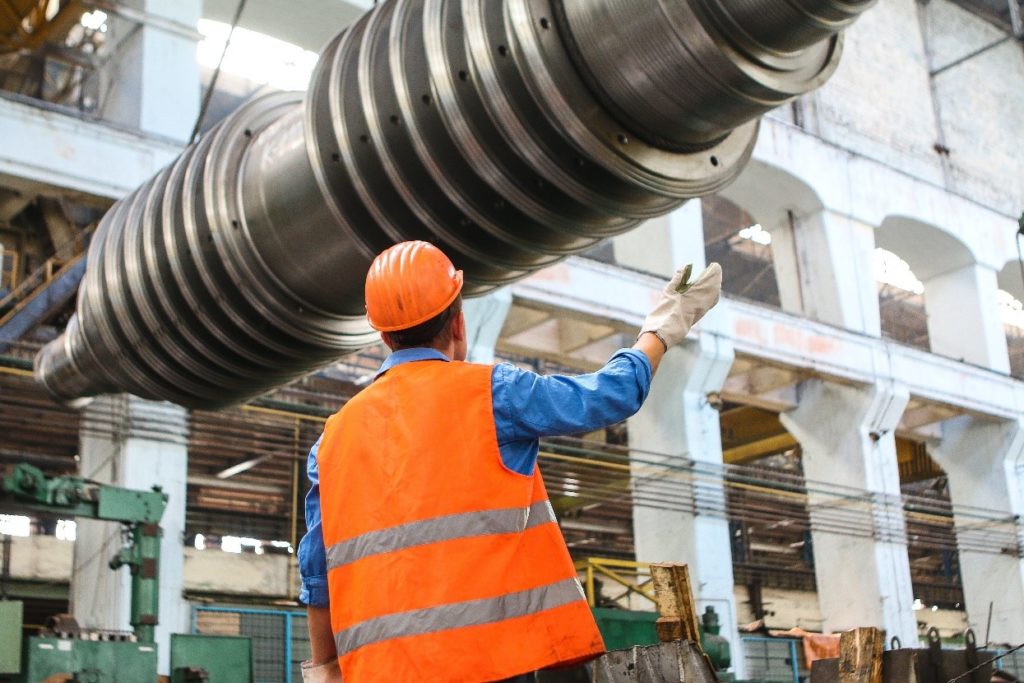
Estimated reading time: 8 minutes
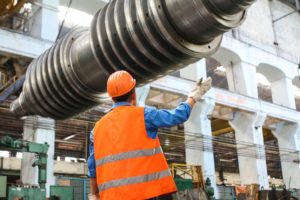
<Why is Maintenance and Reliability Management Important?>
Maintenance and reliability management play a very crucial part in any well-functioning production. They help provide the appropriate maintenance on the right assets at the right time. According to study by Mckinsey, it can reduce machine downtime by 30%-50%, and increase machine life by 20%-40%. It also plays a significant role in determining the success and longevity of the organisation. It helps organisations put their resources to best use and ensure maximum efficiency as well as safety in the workplace.
Why Maintenance and Reliability Management is Important:
- Improve Equipment longevity
- Improve Production quality and quantity
- Reduce Production cost
- Improve employee satisfaction
- Survive Competition
- Scheduling
- Improve Customer Satisfaction
Improve Equipment longevity
The maintenance and reliability management team helps to deliver a proper balance of maintenance activities primarily those aimed at identifying impending failures. This will be to allow for timely corrective actions. Timely maintenance improves the equipment longevity and keeps the production line running smoothly
Improve Production quality and quantity
When organisations don’t have a dedicated maintenance and reliability management team to carry out proper timely maintenance, the chances of breakdown increases significantly. This in turn affects the production of the organisation. On top of that, poorly maintained equipment will very often produce low quality products. Regular maintenance helps to keep the machines/equipment in their optimum operating conditions.
Reduce Production cost
Labour cost really adds up when a particular machinery is sitting idle due to breakdown. When machine malfunctions result in scrap, downtime costs and material costs increases as well. Regular maintenance helps ensure that such scenarios never happen
Improve employee satisfaction
One of the first advantages that come to mind when we think about reliability and maintenance management is improved productivity and cost cutting benefits. But it also has a lot of positive effects on the maintenance workforce of the organisation. It reduces the risk of injury, increases satisfaction and morale. This provides the employees with freedom to develop professionally. On top of that, it also helps the employees to work more efficiently and effectively as they will have fewer disruptions or concerns that break their focus and productivity.
Survive Competition
With rising competition, managers are under constant pressure to find new and better ways to contain and control the cost of doing business. When an equipment doesn’t go through maintenance for a long time, it suffers a breakdown. The cost of repair of this equipment will be very high which drastically affects the profitability of the organisation. Therefore, managers should focus on improving the efficiency of maintenance.
Scheduling
With the advancement in technology there are softwares to help schedule maintenance in an effective manner. Scheduling work is a major task of the manager where he needs to assign all the resources of labour and time in the best possible way. Therefore, the manager requires having a thorough knowledge on the way in which the company works. He, with the help of a maintenance management program sets priority levels on different kinds of equipment and their activities.
Improve Customer Satisfaction
If a production is halted due to equipment breakdown, it affects the deadline of the production. Production delays leads to delay in delivery of those products to the clients and customers which affects the company reputation as well as customer satisfaction. A good maintenance and reliability program will help ensure that these production halts are minimized so that the customers are served well in time.
Equipment reliability can largely depend on the types and techniques used. While there are a number of them, the techniques which are used widely are listed below:
- Reliability Modelling
- Failure Modes and Effects Analysis (FMEA) and Failure Modes and Criticality Analysis (FMECA)
- Reliability Centred Maintenance (RCM) and PM Optimisation (PMO)
- Root Cause Analysis
No matter what field you are in, one of the most important aspects of running an organisation is making sure that every component runs as smoothly as possible. Setting up the right reliability and maintenance program will help ensure that all the facilities in the organisation are running optimally which can bring about as much as a 7:1 return in the first year alone.
It is clear that having an organized and efficient maintenance and reliability management system reduces the number of machine breakdowns ultimately minimises losses from halt in production or unplanned plant shutdowns, contributing to the success of the organisation.