Considerations for Combustion Optimisation in Direct Fired Heaters
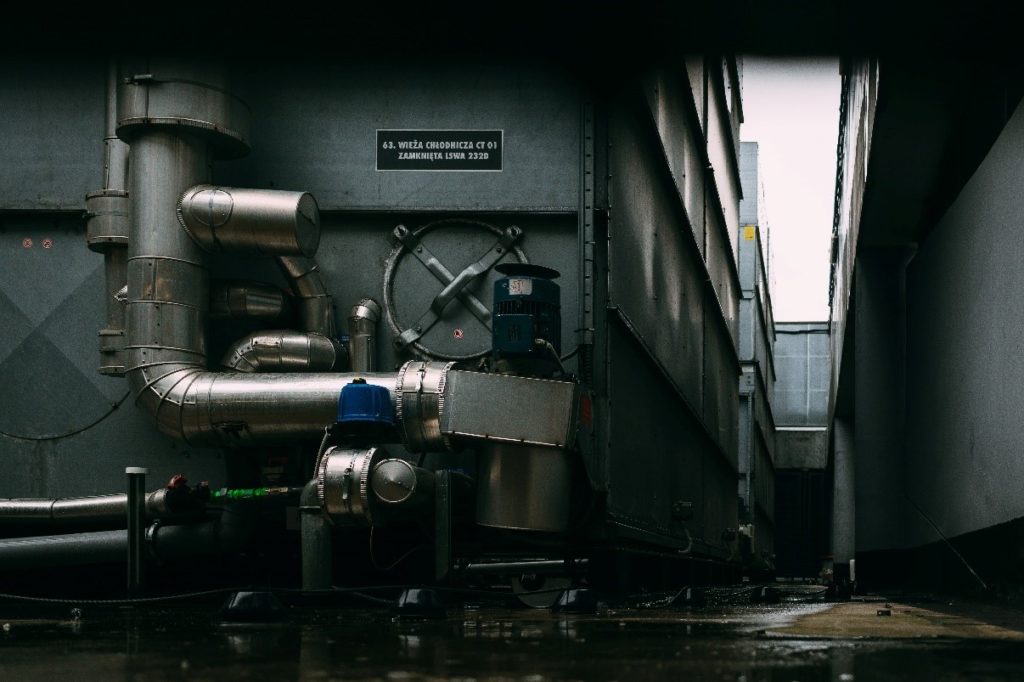
Average reading time 6mins
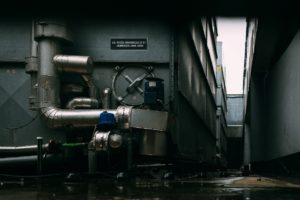
<Considerations for Combustion Optimisation in Direct Fired Heaters>
When process engineers mention optimisation processes in Direct Fired Heaters, they often refer to the optimisation required in the combustion part. Combustion optimisation for Direct Fired Heaters is an important concept since the performance objectives of process heaters are traditionally to maximize heat delivery of the process-side feed while minimizing fuel consumption and maximize heat delivery with varying fuel quality. There are 2 main considerations during the combustion optimisation process in Direct Fired Heaters.
The two main factors that will influence the combustion optimisation process are: Nitrogen levels and fuel air quantity.
Nitrogen Levels
While oxygen (O2) is one of the most common elements which make up 20.9% of the air in our environment, the other 79% of our air largely comprises of nitrogen. In fact, Nitrogen is a temperature reducing diluting agent, which unfortunately must be present in the combustion process in order to obtain the necessary oxygen required for combustion. For every part of oxygen, four parts of nitrogen enter the burner.
Nitrogen reduces combustion efficiency by absorbing heat from the combustion of fuels and diluting the flue gases. As the nitrogen is non-combustible, it absorbs the heat and carries it to the stack. This reduces the heat available for transfer through the heat exchange surfaces. It also increases the volume of combustion by-products, which then travels through the heat exchanger and up the stack faster to allow the introduction of additional fuel air mixture.
This nitrogen can also combine with oxygen, at high flame temperatures to produce oxides of nitrogen (NOx), which are toxic pollutants when emitted into the atmosphere. Therefore, it is extremely crucial for process engineers to be able to control the amount of nitrogen present in the combustion process to maintain efficiency of the heater.
What we can do about it
Low excess air firing (LEA) is the simplest way to reduce NOx formation and improve efficiency. The more excess air, the more oxygen is available to produce NOx. Low NOx burners stage the combustion as it controls the flame temperature and reduces oxygen concentration or residence time making it is possible to cut NOx emissions.
Another method would be flue gas recirculation. This method involves blowing external flue gases into the combustion air, in order to lower the flame temperature and cut formation of NOx.
Fuel Air Quantity
Air-to-fuel ratio defines the amount of air needed to burn a specific fuel. For any combustion process there is a balance sought between losing energy from using too much air and wasting energy from running too richly. Therefore, studies have shown that the best combustion efficiency occurs at the optimum air-to-fuel ratio and controlling this provides the highest efficiency. While trying to stop excessive air from entering the combustion, the amount of air mixed with fuel can be less than required.
This can lead to incomplete combustion where the fuel leaves the stack without being ignited, resulting in a loss of energy as well as a lack of oxygen during the combustion process which creates CO and NOx emissions. Therefore, for process engineers, it is important to be equipped with the relevant knowledge required to carry out such efficient combustion process, since maintaining the balance between air and fuel is an extremely technical task to perform.
What we can do about it
In the combustion zone, it is difficult to measure excess air. However, in the stack, it can be easily measured using Oxygen Analysers. Oxygen analysers are tools used to provide data which help process engineers control the fuel-air ratio in the combustion process. The fuel-air ratio in the combustion process is crucial when optimizing combustion and boiler efficiency. The ideal air-to-fuel relationship will vary at different operating loads. When operating with 5%-20% excess air, it would correspond to a 1% to 3% oxygen measurement in the stack. Through the use of Oxygen analysers, the fuel to air ratio can be achieved with much ease.
Another method to control the fuel to air ratio would be to use Ratio Control system as seen in Figure 1 below.
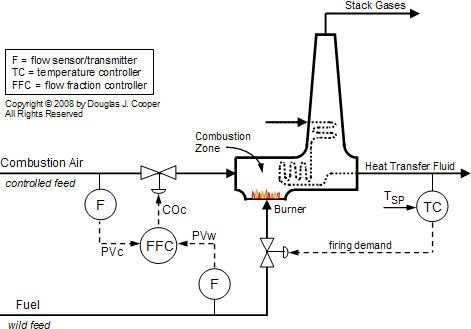
<Direct Fired Heaters – Ratio Control System>
These systems are usually automated to adjust flow rates to maintain the temperature of the heat transfer fluid exiting a furnace. The temperature controllers present in the system maintains the amount of fuel entering the combustion process. The flow sensors then send the flow rate data to the flow fraction controller (FFC), which then calculates the required amount of air present and changes it accordingly. This would therefore help increase combustion efficiency and decrease harmful emissions into the environment.
Direct-Fired Heaters: Their Design & Operation is a 3-day course crafted to allow plant engineers to better understand the function of direct-fired heaters. On top of that, the trainers would go in-depth into how engineers can improve these heater designs to increase efficiency of the heater and benefit the plant.
Interested to find out more?